Automatisierung, Digitalisierung, Künstliche Intelligenz: Die Herausforderungen des Maschinen- und Werkzeugbaus waren in den letzten Jahren durchaus mannigfaltig. Aber dies waren bei Leibe nicht die einzigen Aufgaben: Die Nachhaltigkeit gewinnt immer mehr an Bedeutung, und der Maschinen- und Werkzeugbau muss sich im Spannungsfeld zwischen Ökonomie und Ökologie verorten. Gleichwohl wäre es falsch, diese Spannung als ein Gegeneinander aufzufassen, vielmehr kann und sollte der Druck als Initial für innovative Veränderungen aufgenommen werden, so ein Kredo des jüngsten Praxisforum Werkzeugbau des Verbands Deutscher Werkzeug- und Formenbauer (VDWF) und der WBA Aachener Werkzeugbau Akademie an der Hochschule Schmalkalden.
Das Motto des Tages mit seinem umfänglichen Programm war: „Der Mensch steht im Mittelpunkt. Die Bedürfnisse von Menschen, ihr Komfort und ihre Interessen sind ein antreibender Motor der Innovationskraft des Maschinen- und Werkzeugbaus in seinen verschiedenen Facetten. Den Alltag bequemer zu machen zählt hier ebenso dazu wie Produkte besser und ökologischer sowie kostengünstig und daher allgemein verfügbar anzubieten. Um diese Ziele zu erreichen, können Instrumente wie die Künstliche Intelligenz helfen.
Die Nachhaltigkeit erhielt in den letzten Jahren mehr und mehr Bedeutung. Gerade weil der Klimawandel und seine Folgen immer deutlicher zutage treten und ins gesellschaftliche Bewusstsein rücken, richten sich Forderungen an die Politik und die Wirtschaft. Allerdings trifft diese Entwicklung den Maschinen – und Werkzeugbau keineswegs unvorbereitet: Der sorgsame Umgang mit Materialien, Rohstoffen und Energieträgern war schon immer geboten und ein wichtiger Aspekt von Entwicklungen und Innovationen, von Hochschulen angewandter Wissenschaften, forschenden Unternehmen und ihren gemeinsamen Kooperationsprojekten.
Gastgeber der Veranstaltung war die Angewandte Kunststofftechnik der Hochschule Schmalkalden, wobei Prof. Dr. Thomas Seul, Inhaber der Professur für Fertigungstechnik und Werkzeugkonstruktion an der HSM und Präsident des VDWF, auch die Aufgabe der Begrüßung übernahm. Hier griff er das Motto „Der Mensch steht im Mittelpunkt“ auf und machte zugleich deutlich, dass auch die Studiengänge Menschen, also engagierte und interessierte Studierende, bräuchte. Um all die technologischen, ökonomischen und ökologischen Herausforderungen angehen zu können, bedarf es gut ausgebildete Problemlöser: Gerade anwendungsnahe ingenieurwissenschaftliche Studiengänge wie die Kunststofftechnik vermitteln im Rahmen des Bachelor- und Masterstudiums Fertigkeiten und Fähigkeiten, die die zukünftigen Ingenieure und Ingenieurinnen in die Lage versetzen, innovative Antworten auf komplexe Herausforderungen zu finden.
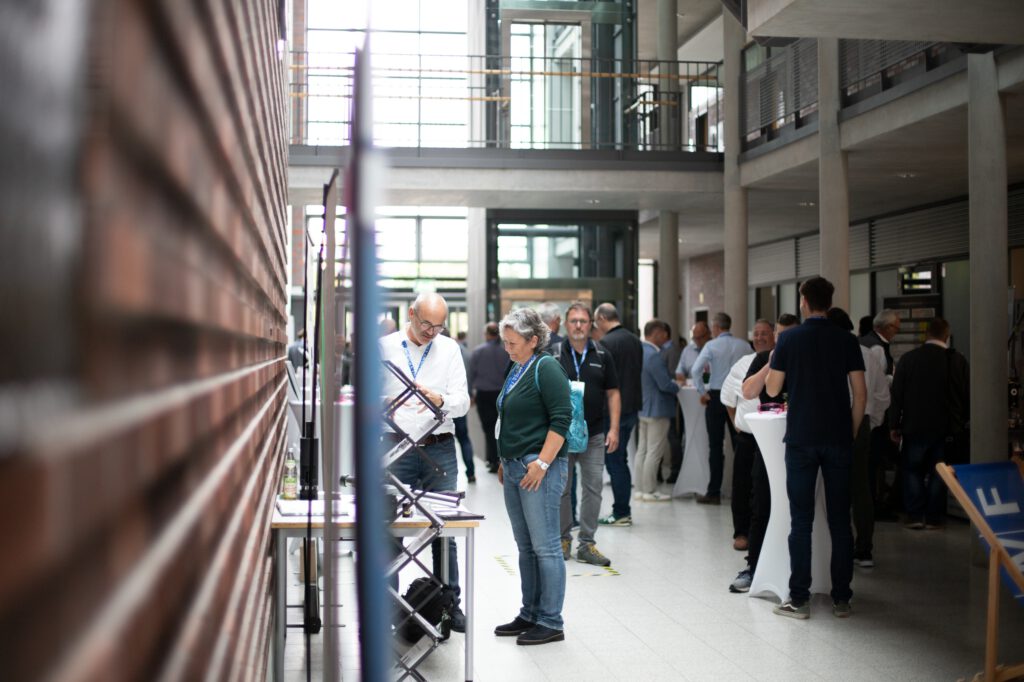
Innovationen, Rezyklate und ökologische Potentiale
Die thematische Ausrichtung der Treffpunkte wechselt mit dem Ort der Veranstaltung, und in Schmalkalden steht traditionellerweise der Spritzguss im Fokus. In den verschiedenen Vorträgen des Tages wurden unterschiedliche Aspekte der Nachhaltigkeit verhandelt: Die Frage war unter anderem, wie wir Rezyklate optimal nutzen, Kreisläufe schließen oder den Energiebedarf gemäß ökologischer Imperative decken können.
Den Anfang machte Frank Schockemöhle von dem Unternehmen Pöppelmann, der sich mit dem Thema «Reduzierung der Treibhausgasemission durch Einsatz von Rezyklaten» befasste. Das Familienunternehmen aus Lohne hat eine nachhaltige Kreislaufwirtschaft ihrer Produktion und Produkte ins Visier genommen und eine mehrstufige Strategie zur Umsetzung konzipiert. Es versteht sich von selbst, dass der Lebenszyklus von Kunststoffen maximiert werden sollte, werden diese Materialien doch in aufwändigen Verfahren gewonnen. Ein Ansatz ist dabei, Kunststoffe zu recyceln und wieder in den Kreislauf zu überführen, wobei auch die EU den Unternehmen aufgibt, entsprechende Mengen an postconsumer-Material, das in anderen Worten schon einmal genutzt wurde, einzubringen. Probleme sind dabei der Aufwand der Aufbereitung und die eingeschränkten Möglichkeiten der Wiederverwendung. Die Wiederverwertung wird umso aufwändiger, je mehr Materialien, also unterschiedliche Kunststoffe oder andere Materialien wie Papier und Metall Verwendung finden. Etiketten oder die Aluminiumdeckel bei Joghurtverpackungen sind hier bekannte Beispiele. Je sortenreiner also ein Objekt ist, umso einfacher die Wiederverwertung: Wichtig ist, dies schon beim Produktdesign selbst zu bedenken. Zum anderen Problem: Zum einen eignen sich natürlich Rezyklate nicht für alle Anwendungen, bleiben doch zumeist Restbestände an farblichen und olfaktorischen Beimengungen. Viele andere Bereiche, in denen zum Beispiel kein direkter Kontakt mit dem Produkt besteht, könnten Rezyklate verwendet werden, dürfen es aber aufgrund der momentanen Gesetzeslage nicht. Hier gäbe es also Stellschrauben. Durch ein konsequentes Design for recycling und eine Anpassung bestimmter Normen ließen sich die Treibhausgasemissionen noch weiter senken. Andere Wege zur Senkung von Emissionen sind die Reduzierung des Materials und die Etablierung echter Kreislaufsysteme von Rohstoffen.
Die Aachener Werkzeugbau Akademie (WBA) ist in den Feldern Beratung, digitale Lösungen, Weiterbildung und Forschung speziell für den Werkzeugbau aktiv. Dr. David Welling, der Geschäftsführer der WBA, arbeitete in seinem Vortrag „Der öko-effektive Werkzeugbau – ökologisch notwendig und ökonomisch erfolgreich “ den Nutzen von Nachhaltigkeitsinitiativen heraus. Zunächst ging es ihm um eine Bestandsaufnahme der gegenwärtigen Situation des Werkzeugbaus, die sich nicht anders als eine multiple und anhaltende Krise bezeichnen lässt. So träfe eine Strategie- auf eine Erfolgskrise, woraus am Ende eine Liquiditätskrise folgen könne. Die Krisenhaftigkeit zeige sich auch an wichtigen Indikatoren wie einer sinkenden durchschnittlichen Marge, einer stagnierenden Wertschöpfung pro Mitarbeitenden und einer sinkenden Quote von Aufträgen ohne Budgetüberschreitung (ab 2019). Neben die ökonomischen Herausforderungen träten nun noch ökologische, wobei Dr. David Welling dafür plädierte, beide Aspekte gemeinsam zu lösen. Der ökologische Druck besteht nicht nur aus der Selbstverpflichtung der EU zur Klimaneutralität und den entsprechenden Maßnahmen, sondern auch aus den Strafen für nichtgemeldete CO2-Emissionen, Berichtspflichten und Nachhaltigkeitsanforderungen. Der Ansatz der Öko-Effektivität zielt darauf, Herausforderungen auf beiden Feldern mit einer Lösung zu begegnen, also beides zusammenzudenken und produktiv zu nutzen. Zum Beispiel regen die hohen Energiekosten zu einem noch effizienteren Produzieren an, was wiederum die Treibhausgasemissionen senkt.

Karosserien und Schäume
Klaus Sammer, Leiter Werkzeugbau, Instandhaltung und Vorentwicklung der Leichtmetallgießerei, und Thomas Kopp gaben einen Einblick in die Entwicklungen beim Karosseriebau bei BMW Landshut: Bei dem Karosseriebau war die Herausforderung schon immer, komplexe und zugleich große Bauteile effizient herzustellen. Das Verfahren des Aluminium-Druckgusses wurde hierbei immer mehr verfeinert: Die in Landshut vor Kurzem entwickelte Mehrplatten-Technologie[i] erlaubt, bei der Konstruktion der Komponenten den Primat von der Optimierung des Fließwegs hin zur Funktionalität zu verlegen. Zugleich lassen sich so Material und Gewicht einsparen, was wiederum zu Einsparungen bei den Emissionen führt. Eine weitere Herausforderung, vor die in der momentanen Lage vermutlich alles Gießereien und Schmelzen stehen, sind die hohen Energiekosten. Durch diesen Druck bietet sich eine Umstellung auf nachhaltige Rohstoffe wie Solarenergie und grünen Wasserstoff an, was wiederum dem Ansatz der Öko-Effektivität entspricht. Natürlich entstehen wiederum Folgeprobleme wie unterschiedliche Temperaturen beim Verbrennen, die Korrosion durch das anfallende Wasser und höheren Verbräuche im Vergleich zum Erdgas: Aufgabe ist es dann, Erfahrungen mit den neuen Verfahren zu sammeln und Lösungen für eventuelle Probleme zu finden. Auch die Elektromobilität ist in diesem Sinne eine Herausforderung, die zu Innovationen anregt: Die Karosserien müssen nun noch komplexer werden und mehr Funktionen integrieren, was wiederum neue Verfahren ihrer industriellen Produktion verlangt. Die Serienfertigung zieht zudem weitere Anforderungen von der Kosteneffizienz bis hin zur Klimabilanz nach sich. Das jüngst vorgestellte „Injector Casting“[ii] Verfahren der Leichtmetallgießerei aus Landshut könnte eine innovative Lösung sein.
Eine andere innovative Möglichkeit zur Einsparung an Material im Kunststoffspritzguss ist das Schäumen. Neben diesem Aspekt bietet dieser Ansatz auch andere Vorzüge, auf die Uwe Kolshorn vom Kunststoff-Instituts Lüdenscheid in seinem Vortrag „Die <andere Denke> beim Kunststoffschäumen – geringere Drücke, Aluwerkzeuge und längere Fließwege, was will man mehr!?“ hinwies. Zunächst sind Schäume keine komplett neuen Bauformen, sondern orientieren sich an den zellularen Formen der Natur. Zugleich ist Schaum nicht gleich Schaum: Verschiedene Materialien und Herstellungsverfahren führen zu unterschiedlichen Eigenschaften und Anwendungsmöglichkeiten. Die grundsätzlichen Vorteile des Schäumens beim Spritzguss sind die geringere Viskosität des Materials (Zähflüssigkeit) und der Verzicht auf den Nachdruck, entsteht der Druck doch im Inneren – eben durch das Aufschäumen. Somit werden unter anderem eine schnellere Füllung und niedrigere Temperaturen des Materials und des Werkzeugs, möglich. Wichtig ist es, bei der Konstruktion der Komponenten bereits die Charakteristika des Schaums im Blick zu haben und die gebotenen Vorteile zu nutzen. Zugleich hat die Verwendung von Schaum auch gewisse Nachteile, mit denen umgegangen werden muss. Beispiele sind die typischen Randausprägungen in Kissenform oder Schlieren auf der Oberfläche. Je nach Anwendungssituation lassen sich hier unterschiedliche Lösungsansätze finden.
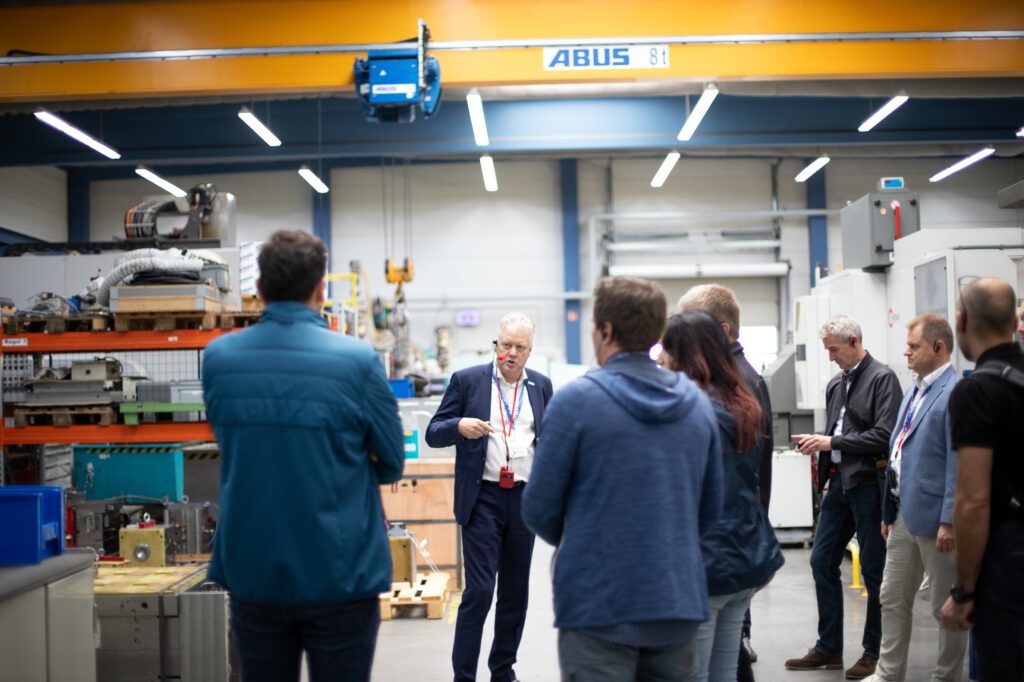
Bewegte Zeiten
Christen Merkle, Geschäftsführer von AHP Merkle, zeichnete in einem lebendigen Vortrag mit dem Titel „Was mich bewegt.“ ein Bild der Situation, in der sich kleine und mittlere Unternehmen wie der Spezialist für Zylinder aus dem baden-württembergischen Gottenheim momentan befinden. Neben der schwierigen Lage der Wirtschaft beschäftigen die Unternehmer der schlingernde Kurs der Politik und der Wandel gesellschaftlicher Einstellungen. Unternehmerische Entscheidungen, zum Beispiel Investitionen, brauchen aber langfristige Planbar- und Verlässlichkeit der Rahmenbedingungen, zum Beispiel der Wirtschaftspolitik. Hier gebe es, vorsichtig formuliert, Verbesserungspotentiale. Die Krisenhaftigkeit der Zeit und die Strukturprobleme wie der Fachkräftemangel beiseite präsentierte sich Christen Merkle als leidenschaftlicher, in der Region verwurzelter Familienunternehmer, der sich seiner sozialen und ökologischen Verantwortung bewusst ist. Ein Beispiel der Vorzüge einer solchen langfristigen Orientierung zeigte sich in der Pandemie: Merkle verzichtete auf Maßnahmen wie Kurzarbeit und setzte auf Forschung und Entwicklung, von der das Unternehmen nun mir erfolgreichen Produkten profizieren kann.
Den letzten Input gab dann Stephan Hoffmann, Geschäftsführer der Formconsult Werkzeugbau GmbH aus Schmalkalden, dessen Vortrag in eine Firmenbesichtigung mündete. Das Unternehmen stellt hochpräzise Werkzeuge her und hat sich auf Mehrkomponenten- und Zweifarbentechnik spezialisiert. Der innovative Werkzeugbau beruhe auf drei Säulen, wobei die Entwicklung, Konzipierung und die Simulierung erste Säule wäre. Neben der Kooperation mit Partner wie der HSM und der GFE sorge hierbei auch die Unterstützung von Start-Ups für die Freisetzung innovativer Potentiale. Die zweite Säule besteht im Werkzeugbau selbst, seiner Spezialisierung und der Fertigung. Aspekten der Nachhaltigkeit könne hier genüge getan werden, indem bei den Produktionsstätten auf Energieeffizienz und die Nutzung erneuerbarer Energien – wo möglich – zurückgegriffen werde, sei es durch Solarpanels oder die Klimatisierung über hocheffiziente Wärmepumpen. Die dritte und letzte Säule ist das Technikum, was der Qualitätssicherung dient. Bemusterung, Vermessung und u.a. die Dokumentation sollen neben einer beständigen Zertifizierung die Qualität der Produktion und der Produkte garantieren.
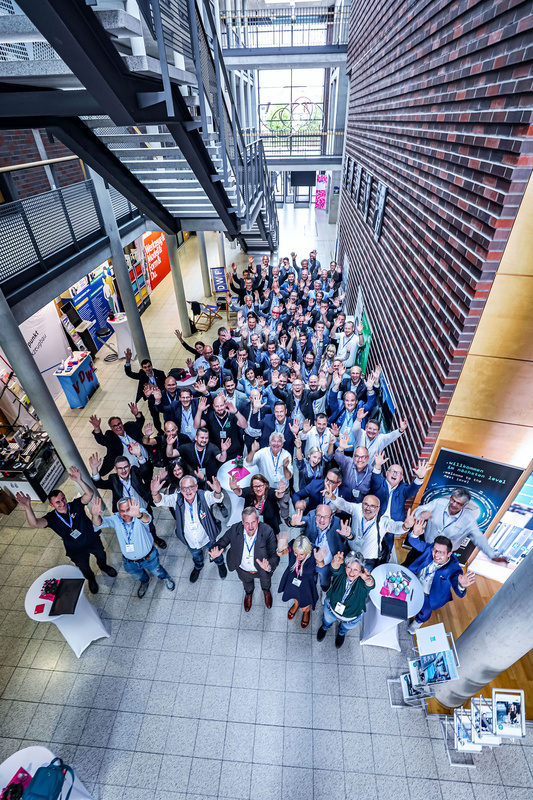
Das Resümee der Veranstaltung legt einen Blick auf den Anfang der Veranstaltung nahe, also die Begrüßungsworte von Prof. Thomas Seul: Sein Plädoyer war die konstruktive Zusammenarbeit von Hochschulen für angewandte Forschung und Unternehmen. Durch diese Kooperation könnte die Expertise der akademischen Forschungsbereiche genutzt werden und so letztlich beide Seiten profitieren. Eine andere Möglichkeit der Zusammenarbeit sind übergreifende Netzwerktreffen wie das Praxisforum, das von Partner aus der Wirtschaft (FDU Hotrunner, HoliMaker, Meusburger, Moulding Expo, Partool und Process Garding) gesponsert und somit in dieser Ausrichtung dankenswerterweise möglich gemacht wurde.
PS: Der Bericht zum vorherigen VDWF-Treffpunkt Werkzeugbau
[i] https://www.aluminium-journal.de/druckguss-bmw-setzt-auf-mehrplatten-werkzeugtechnik
[ii] https://www.bmwgroup-werke.com/landshut/de/aktuelles/2023/erster-guss-in-neuer-high-tech-leichtmetallgiesserei.html