Research at universities of applied sciences is practical and transfer-oriented: The potential of mutual cooperation between science and industry can be clearly seen in research projects such as Extrusion Molds in Additive Manufacturing – ExAM, which Stefan Roth, Professor of Product Development and Design at HSM and part of the Applied Plastics Technology (AKT) team, is currently implementing.
What is it all about? First of all, it makes sense to introduce extrusion as a special process in plastics technology: Basically, extrusion is a way of manufacturing “endless” plastic parts such as pipes and hoses, although the actual method is also used in other contexts, for example in the production of pasta. In short, an extrusion line can be described as an apparatus that liquefies raw materials such as plastics, metals or foodstuffs and presses them through a nozzle – also known as a die – whereby this opening produces the shape of the product. In contrast to other processes, the outlet is continuous, which in turn brings with it specific possibilities, but also challenges. It is important to note that the complexity goes beyond the die and includes process steps such as cooling in addition to the melt. Before we turn our attention to the ExAM research project, which focuses on the advantages of additive manufacturing of tools such as the nozzle, we will first remain with the extrusion process.
The extrusion
As already mentioned, extrusion is not a single machine, but can rather be understood as a system with various parts and stations. Let’s take a brief look at the path of the product: At the beginning is the raw material, i.e. the granulate, which is fed into the extruder via a hopper. This contains a screw that rotates and transports the material to the outlet, mixing, compacting and heating it in the process. The friction of the material generated by the screw movement produces heat, which melts the granulate. This melting process is promoted by heating belts attached to the outside of the system.
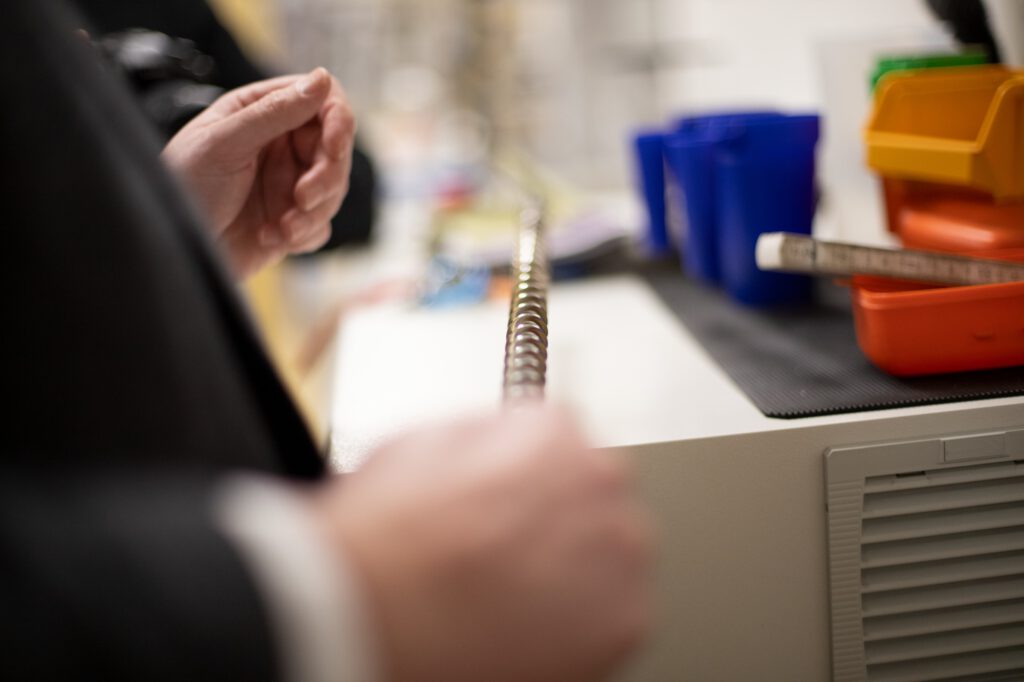
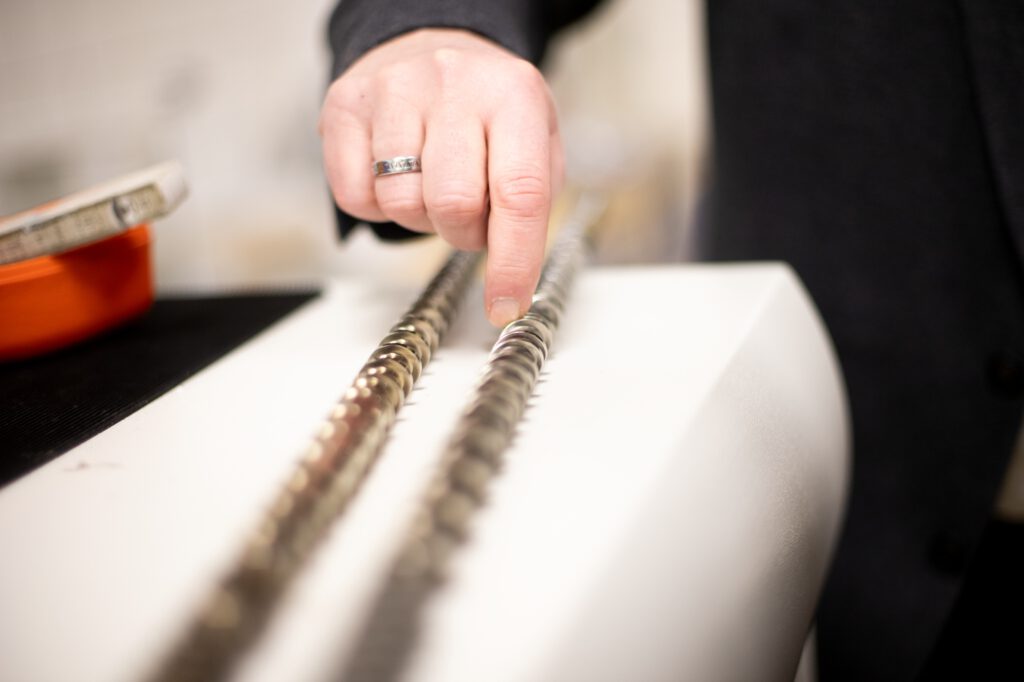
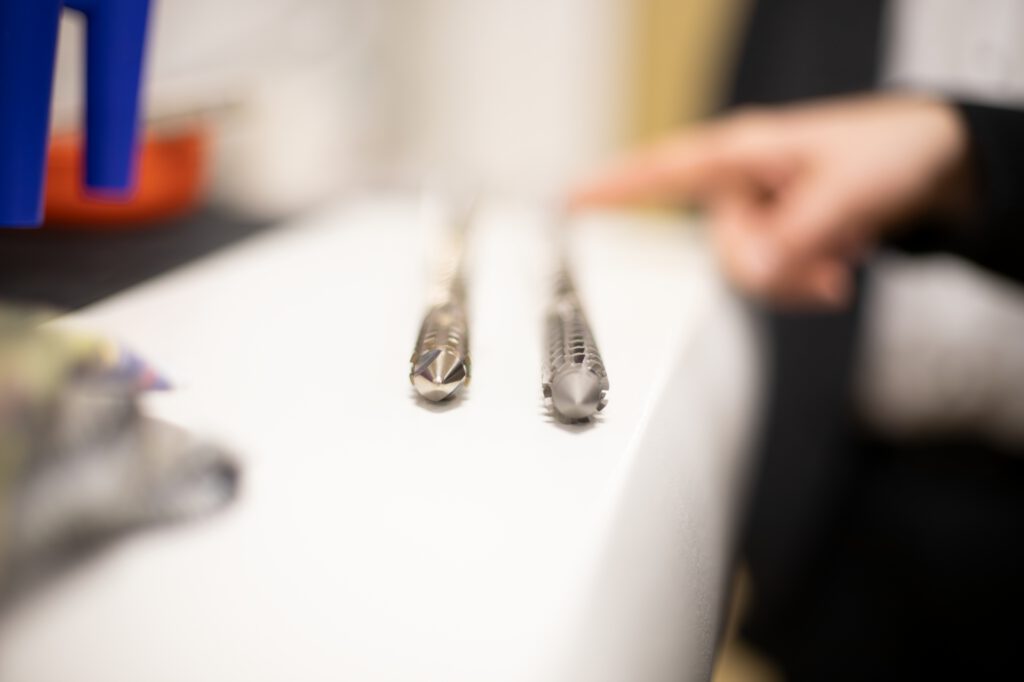
This creates a melt, which is then kneaded and homogenized by the screw. The melt is then pressed through the nozzle and shaped into the desired form. The result is a basically endless molded part, as we know it, for example, as a cable duct, window profile or film. The product is then cooled and simultaneously calibrated, whereby the processes differ depending on the characteristics of the product. The task is to avoid deformation caused by the thermoplastic properties of the material during cooling. At the end of the process, the continuous extrudate is cut to length or wound up.
Optimization approaches
It is important to understand that it is not about a material, a process and a machine that ultimately creates a product, but that various parameters have a decisive influence on the possibilities and limits of the process and the product as well as its quality. For example, both the screw types and their processes (e.g. their rotation) have an impact on the melt: different screw types are suitable depending on the material. There are also variables such as quantity, speed and heat, as well as the role of additives, i.e. additives in addition to the granulate, which in turn have their own properties. All of these components must be coordinated depending on the material and product in order to achieve the most precise and efficient production possible at the end of the process. Especially for products that are typically manufactured by extrusion, the aspects of quantity are central. Due to the high quantities, improvements in production have enormous effects here.
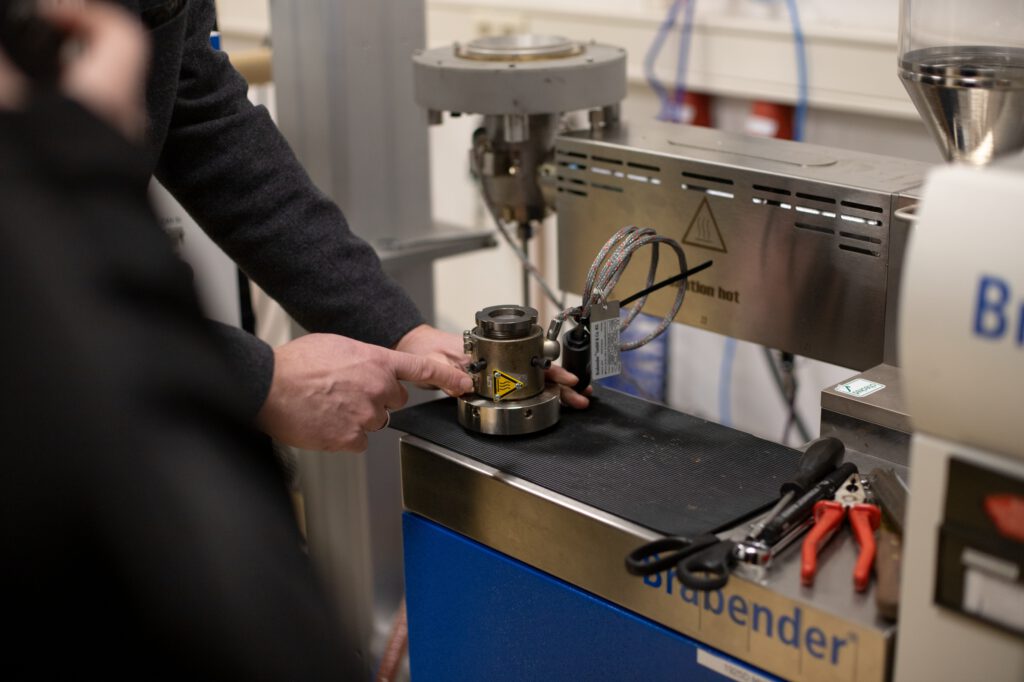
In such fundamental and generalizable areas, joint industrial research is a suitable vehicle for research projects. All participants can benefit from industrial collective research, IGF (Industrielle Gemeinschaftsforschung), projects and their results – without being held back by competitive pressure. In other words, this is an ambitious, pre-competitive cooperation that promotes research for mutual benefit. This community is supported by the Federal Ministry of Economics and Climate Protection and currently brings together 101 research associations and 1,200 research institutions. One of these research areas, represented by the Research Association of German Toolmakers, Forschungsgemeinschaft Deutscher Werkzeug- und Formenbauer FDWF e.V., concerns the question of whether and how the advantages of additively manufactured tools can be measured in the extrusion process. And that brings us to Schmalkalden University of Applied Sciences.
The research project
The ExAM research project shifts the focus away from conventionally manufactured tools, which are produced subtractively, i.e. cutting machining process, towards the process of additive manufacturing. This is already established in other areas – both in general and in the field of plastics production – and now the question arises as to whether these advantages can be transferred to the extrusion process. One obvious benefit is that additive processes offer more degrees of freedom in the production of tools, thus enabling new and innovative approaches to design.
Traditionally, the tools are manufactured using machining processes such as milling, turning or electrical discharge machining. A necessary consequence of this procedure is restrictions such as transitions and dead spaces, which have a negative impact on the flow of the melt. The layer-by-layer structure of additive manufacturing can avoid precisely these restrictions. The optimization of the tools then leads to an improvement in the products and the manufacturing process: better component properties and more dimensionally accurate parts are just as much goals as the more robust and simpler design of the processes. Among other things, the optical properties can be optimized and part rejects minimized. In short, engineers have more options when it comes to design: However, the question of whether the additional expense of additive manufacturing is worth it remains unanswered.
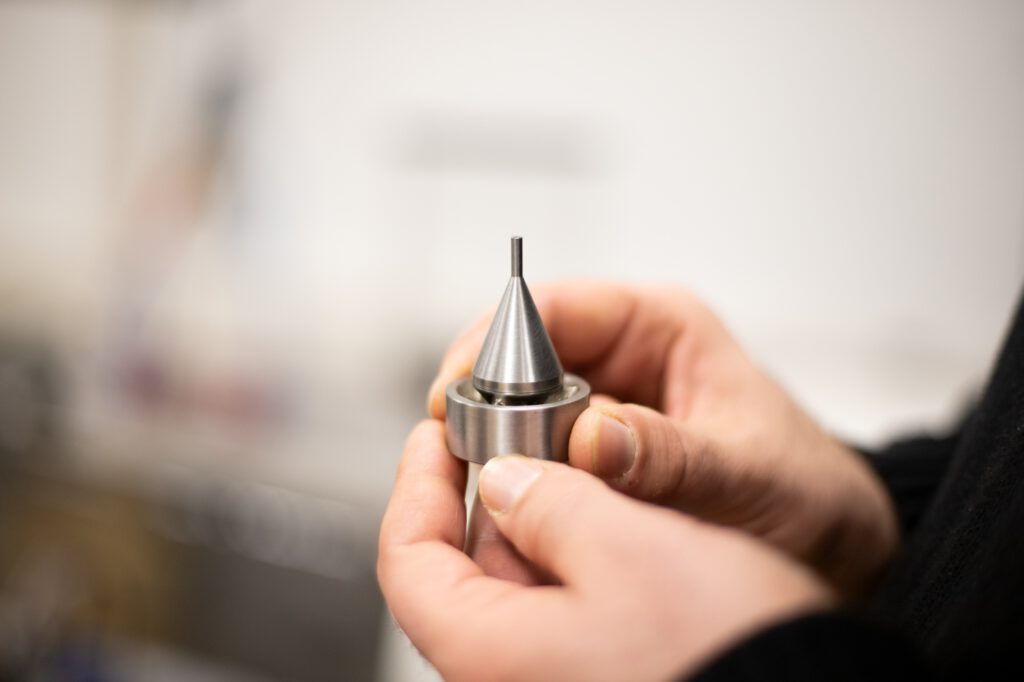
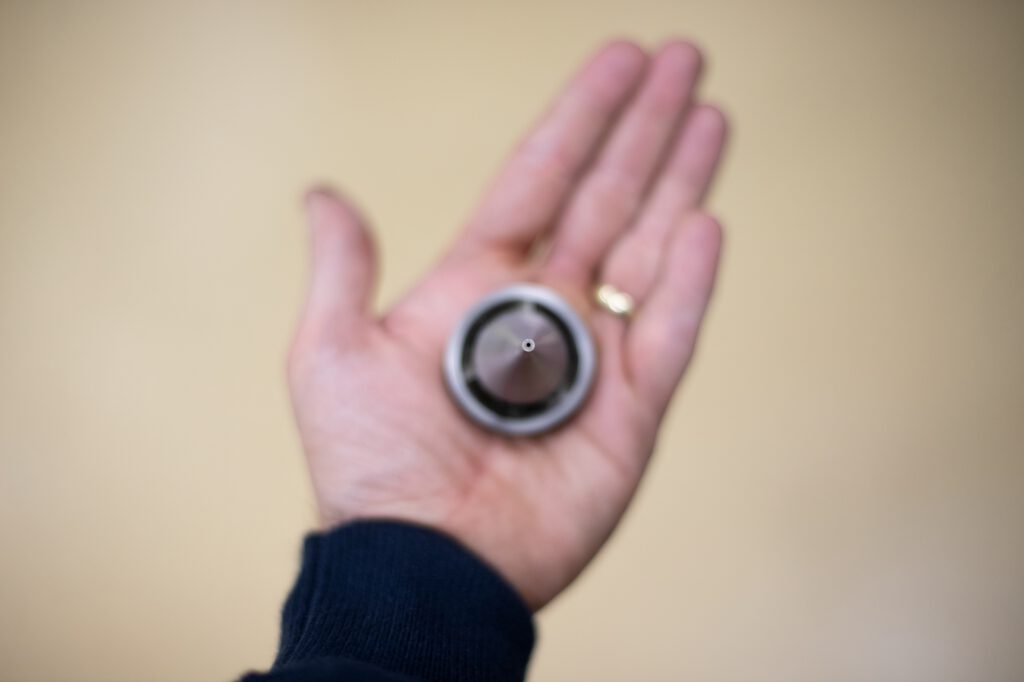
Let’s focus on the possibilities: The central point is the guidance of the melt in the mold, which should be guided as homogeneously as possible to the exit point and brought into shape. Stagnation, jams and dead spaces must also be avoided in terms of material quality, as these lead to streaks or color defects, among other things. The material that accumulates in dead spaces degrades over time, disrupts the flow and has negative effects on the mechanical and optical properties of the material. It is also important to control the speed of the melt, which in turn depends on the pressure and temperature. Additive manufacturing of the tools allows the implementation of targeted temperature control and therefore the best possible design of the melt channels and guidance. At the same time, innovative geometries in the form of cooling channels can be introduced into the tool.
The aim of the design is to optimize the melting chamber, allowing the fastest possible throughput while maintaining the same quality. The increase in efficiency can offer decisive advantages in mass production. This economic benefit in production, which additive components provide, is to be clarified in the ExAM research project. At the end of the project, in addition to evaluating the advantages, a guideline will be developed which will prepare the design and layout of additively manufactured components and be available to all cooperation partners. The companies can then use these guidelines to develop additive tools according to their own requirements and objectives. This basic accessibility means that the technology of additive manufacturing of tools can be widely applied, and the innovative impetus can be used to increase product quality features.
Innovative transfer
The use of additively manufactured and optimized tools is by no means new territory in the field of injection molding, but it is for the extrusion process. It is therefore less important to develop new technologies than to transfer existing ones to a new area. In this way, existing experience from injection molding can be used in aspects such as temperature and flow control of the melt. As a result of the fundamental application orientation, this topic lends itself as a cooperative project of industrial joint research (IGF), whereby all participating companies should be able to benefit from the technologies researched. As a project located here, the focus is on application proximity, i.e. the envisaged competitive advantages of the cooperating institutions and companies.
The two-year ExAM project started last fall and brings together three cooperation partners with three different spotlights: Schmalkalden University of Applied Sciences is focusing on extrusion and the field of health tech; Plastics Technology at Paderborn University is concentrating on the technical profile; and the Fraunhofer Institute for Additive Production Technologies, based in Hamburg-Bergedorf, is specializing in the project on the topic of simulation and additive manufacturing of tools using the laser-based powder bed process.
The variety of shapes in the design made possible by the additive process is a challenge for HSM, as it opens up many new options. At the same time, however, this is also where the innovative optimization of the tools comes in. In addition to the actual shape of the component, various tool steels for the additive laser melting process are also being investigated, whereby the focus is always on types that are already commercially available. It is important that the subsequent use is uncomplicated. Last but not least, each individual optimization must take into account the entire process of the extrusion system and consider possible interactions.

The Faculty of Mechanical Engineering and its research group of applied plastics technology (Angewandte Kunststofftechnik AKT) recently announced a new acquisition that can also support research on the ExAM project: The innovative 3D printer from the manufacturer NewAIM3D was successfully put into operation and is now available for research and teaching. This printer, based on the pellet direct extruder principle, makes it possible to directly and efficiently process plastics and compounds in commercially available pellet form. For example, printing with pellets consisting of metal powder and binder, so-called feedstocks, is possible. The resulting components are then sintered to achieve the density and properties of conventional steels. The process thus represents an alternative to the established but costly additive laser melting process for metal powders. The acquisition of the printer was made possible as part of the third funding period of the Thuringian Center for Mechanical Engineering and was funded by the Thuringian Ministry of Economic Affairs, Agriculture and Rural Areas. The Free State of Thuringia also supports the project, which is co-financed by the European Union as part of the European Regional Development Fund (ERDF).